The extent to which polymers are affected by exposure to chemicals can be influenced by a number of factors. These include: the composition of the polymer (its chemical composition, the presence of fillers and additives); the degree of crystallinity of the polymer; the exposure conditions: time, temperature and pressure; whether the polymer itself is subject to stress: either externally applied or internal stresses from processing; and of course, the nature of the chemical itself – acid, alkali, organic, inorganic, aromatic, aliphatic and so on.
Exposure of a polymer to a chemical can result in either a chemical or a physical interaction of the small molecule (chemical) with the polymer.
- Adsorption is an interaction of the chemical with the surface of the polymer.
- Absorption is the dispersion of the chemical throughout the polymer via (typically) the mechanism of diffusion, which is the penetration of the chemical into the polymer.

Physical and chemical interaction
Physical interaction can often result in the polymer softening (also known as plasticizing) and swelling as the chemical penetrates the free volume of the amorphous regions of the polymer. In semi crystalline polymers, the crystalline regions of polymers have lower free volume and therefore semi crystalline polymers are less susceptible to small molecule diffusion and absorption. In many cases, removal of the chemical and subsequent drying of the polymer may allow it to return close to its original state.
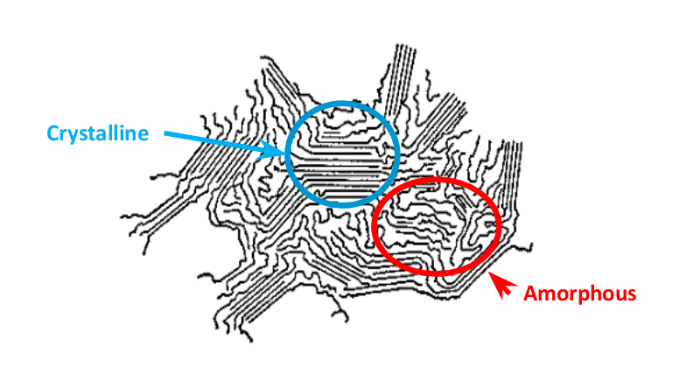
However, if the absorbed chemical is able to act as a solvent to dissolve and remove some of the low molecular weight fraction of the amorphous phase upon drying, the removal of this low molecular weight polymer fraction can lead to embrittlement of the polymer, yielding a significant permanent change in polymer properties. Solvents may also ‘wash’ additives such as plasticizers and stabilizers from a polymer over a period of time.
Chemical interactions with the polymer generally can lead to cross-linking (thereby increasing molecular weight) or degradation / chain scission (decreasing molecular weight). These interactions are generally irreversible and may result in large, permanent changes in the properties of the polymer.
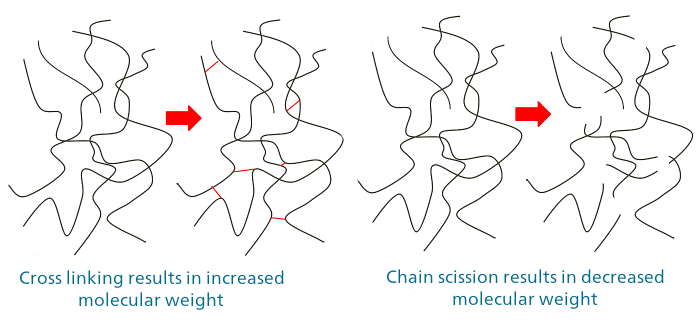
Environmental stress cracking, ESC
When chemical exposure occurs in the presence of stress – most typically an externally-applied stress – then stress cracking leading to polymer fracture can occur. Environmental stress cracking (ESC) is the result of a physical, rather than chemical, surface interaction under stress: there is no chemical transformation but the stress-cracking agent accelerates the formation of macroscopic brittle fractures.
While it is not possible to predict which chemicals can cause ESC, it is generally the case that surfactants are the most effective stress cracking agents. ESC is analogous to the phenomenon of stress corrosion cracking in metals. VICTREX™ PEEK is understood to be largely immune to ESC.
Deep dive necessary
To summarize, to develop innovative and technologically pioneering solutions, chemical resistance testing of polymers for use in an Oil and Gas environment is a very important aspect; but it is just one, especially if the overall objective is predicting thermoplastic composite pipe lifetime in aggressive service environments, where the degradation of the polymer matrix cannot be seen in isolation. Additional mechanisms that need to be considered include the degradation of the fibre reinforcement, of the fibre / matrix interface and of the interface between adjacent lamina, all of which are considered in the upcoming blog post mentioned above.
About the author
Dr. Geoff Small, Market Technology Manager – Victrex
Having studied Materials Science at the University of Bath and obtaining his PhD on the subject of Cellular Composite Structures, Dr. Small has worked in the polymer industry for 23 years. Prior to joining Victrex he worked for The National Physical Laboratory (UK) and for Phillips Petroleum Company in a market development role for engineering polymers.
LinkedIn